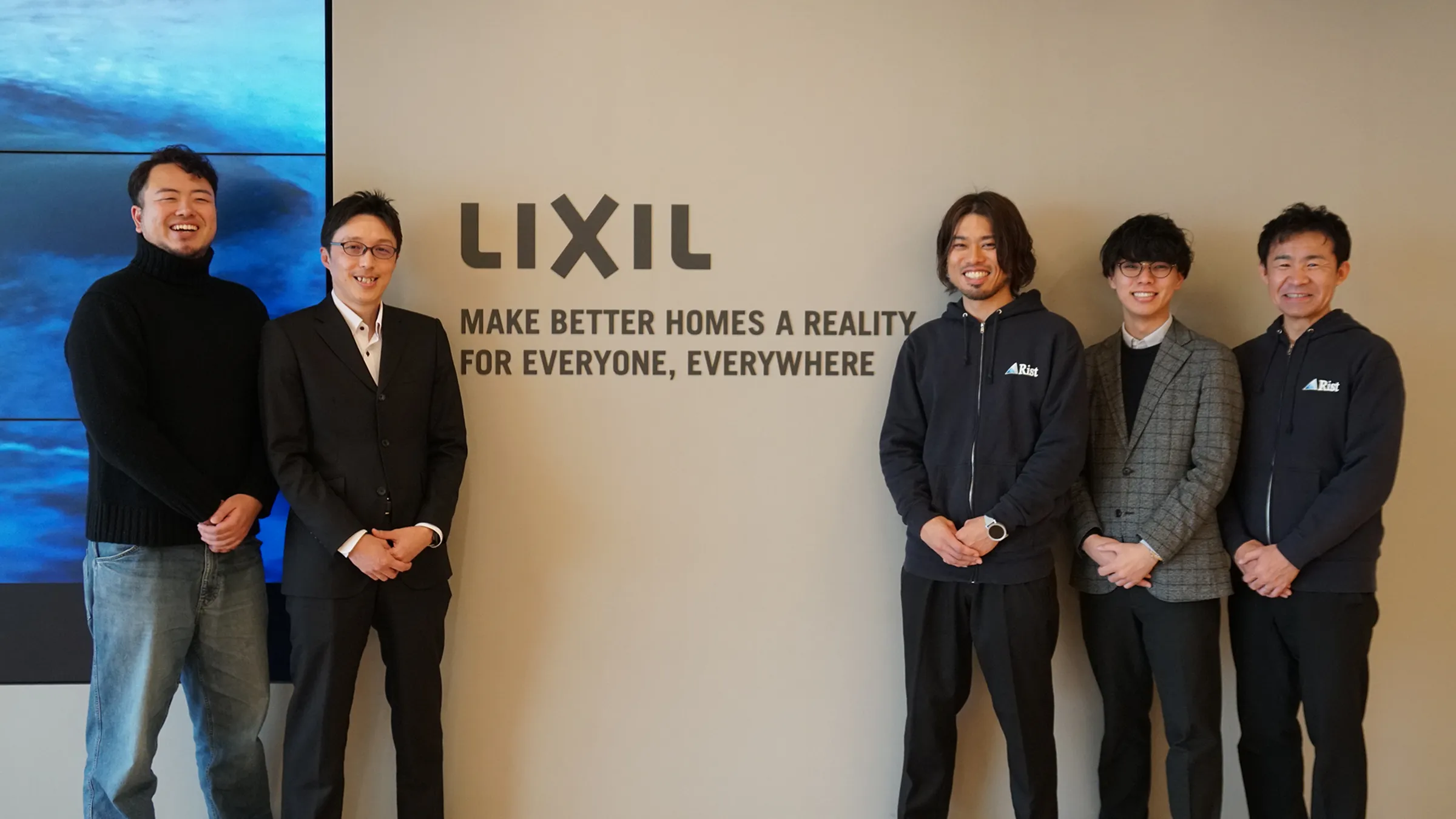
株式会社LIXIL
LHT 生産本部 生産プロセス推進統括部 生産デジタル推進部 デジタル化推進G 開発T 楠野 良樹 様
LHT 名張工場 管理課 神野 和夫 様
株式会社Rist
企画戦略部 Senior Expert 兼 フィールドエンジニアリングチーム Senior Manager 石井 良
セールス・コンサルティング部 マーケティングチーム Manager 村上 義和
京セラコミュニケーションシステム株式会社
ソリューション営業統括部 デジタルソリューション営業部 デジタルソリューション営業課 新谷 正太
建材及び住宅設備メーカー大手である株式会社LIXILでは、「デジタル民主化」をテーマに掲げ、自社内でのアプリ開発によるDX推進に注力してきました。現場社員約10,000人近くがノーコード開発を実践し、その中でも約4,000個のアプリが実際の業務で利用されております。
その中の1つに、アルミ製の部材を自動カウントするアプリがありましたが、ノーコード開発では部材の検出精度に限界があり、複雑な形状の部材は人の力でカウントしていました。そんな時、ある展示会を通じてRistのDeep Counterを知り、オリジナルアプリのエンジンとして搭載することになりました。
プロダクト同様にプロセスにおける技術開発も重視するLIXIL
―まずは、LIXILの事業についてご紹介ください。
楠野さま:私たちは、水まわりをはじめとした住まいのあらゆる製品、建材製品を開発・提供しているグローバル企業です。みなさんもきっと、住宅やビルなどさまざまな建物で「LIXIL」をご覧になったことがあるのではないでしょうか。
今回お話するのは、建材に関わる部門での取り組みについてご紹介します。現在LIXILでは、カーボンニュートラルの実現につながる製品の開発・提供に注力しています。使っていただいて快適で、豊かな暮らしができる製品はもちろん、地球にとっても良い製品を作っていきたいという想いがあります。
一口に建材と言っても、こうした想いを込めて製品づくりをしているメーカーである点を知っていただけると大変うれしく思います。
神野さま:中でも、いま着手しているのが、「revia(レビア)」というブランド名でリリースしている、廃プラスチックを主な原料とした製品です。再資源化が困難だった廃プラスチックに廃木材を融合させ、新素材として現在公園や事業所の敷地などの舗装材として活用しています。SDGsにつながるため環境の観点から見ても魅力ある製品であり、国内にとどまらず海外からの評判も大変良い取り組みです。
通常、LIXILが海外の展示会に出展しても、ドアや玄関の規格サイズが日本と海外で異なるため、なかなか大きな反響を得られません。ですが、環境意識の高い海外では循環型ビジネスへの関心が非常に高く、今後もこうした分野に力を入れて、新たな製品を生み出していく考えです。
楠野さま:レビアを使った第一弾製品として、歩道・広場・公園・建築外構などに使われる舗装材「レビアぺイブ」が発売されており、2025年日本国際博覧会(通称、大阪・関西万博)のあるパビリオンでも採用されるなど、多くのところで実績が生まれています。
神野さま:一方、社内に目を向けてみると、LIXILでは「デジタル民主化」をテーマに掲げDXを推進しています。これまでDXは、限られたスキルを持つ人だけのものだと思われる傾向がありました。ですが、LIXILでは工場や現場社員からデジタル技術に触れ、DXをみんなのものにしたいと考えがあります。
例えば、帳票のデジタル化。手書きからスマホ入力に移行することも、立派なDXです。これからお話するカウントアプリも同様で、LIXILはモノを作るメーカーでありながら、全社的に新たな技術の導入や発展も重視している企業です。
最新技術を調査し、工場のデジタル化推進に取り組む
―楠野さまと神野さまの社内での役割を教えてください。
楠野さま:私の所属は、窓サッシや玄関ドア、カーポートなどの金属製品を取り扱うLHTの生産本部 生産デジタル推進部と言いまして、さきほど神野がお話をしたように、製品そのものではなく、製品を作るプロセスにおける技術の開発や発展に関わる仕事をしています。
分かりやすく言えば、日々さまざまなテクノロジーが生まれ進化していく中で、自社にどのように取り入れられるかを考えています。そのため、いろいろな技術展示会などに足を運んで、自社に役立つ技術を探すのも仕事です。DXの推進では、新しいテクノロジーを製造現場に導入できるよう、工場のメンバーと一緒に開発しています。
神野さま:私は、建材のなかで玄関ドアや室内のインテリア建材を主に製造る三重県名張市にある名張工場で、生産管理や在庫管理、さらに資材調達の仕事をしています。メインの仕事は、購買品関連全般です。製品に使う部品や材料を管理していますが、業務効率化を図るために、新しい技術の導入を推進している立場でもあります。
―日常業務において、AI技術やデータ分析とどのように関わっていますか?
楠野さま:製造領域のデジタル化を推進しています。デジタル技術を用いた業務改善を企画・開発し、工場でのモデル実施まで行います。
神野さま:名張工場における管理業務で、AIを使った安全改善や出庫予測などを手掛けています。DXで大切なのは、世の中の情報をキャッチアップすることです。社内の事情や専門的な部分に詳しいのは当然として、外部の情報をいかに早くつかんで、自社工場に置き換えて使えるかどうかを判断するため、工場の関係者とは常に意見交換・情報共有を図っています。
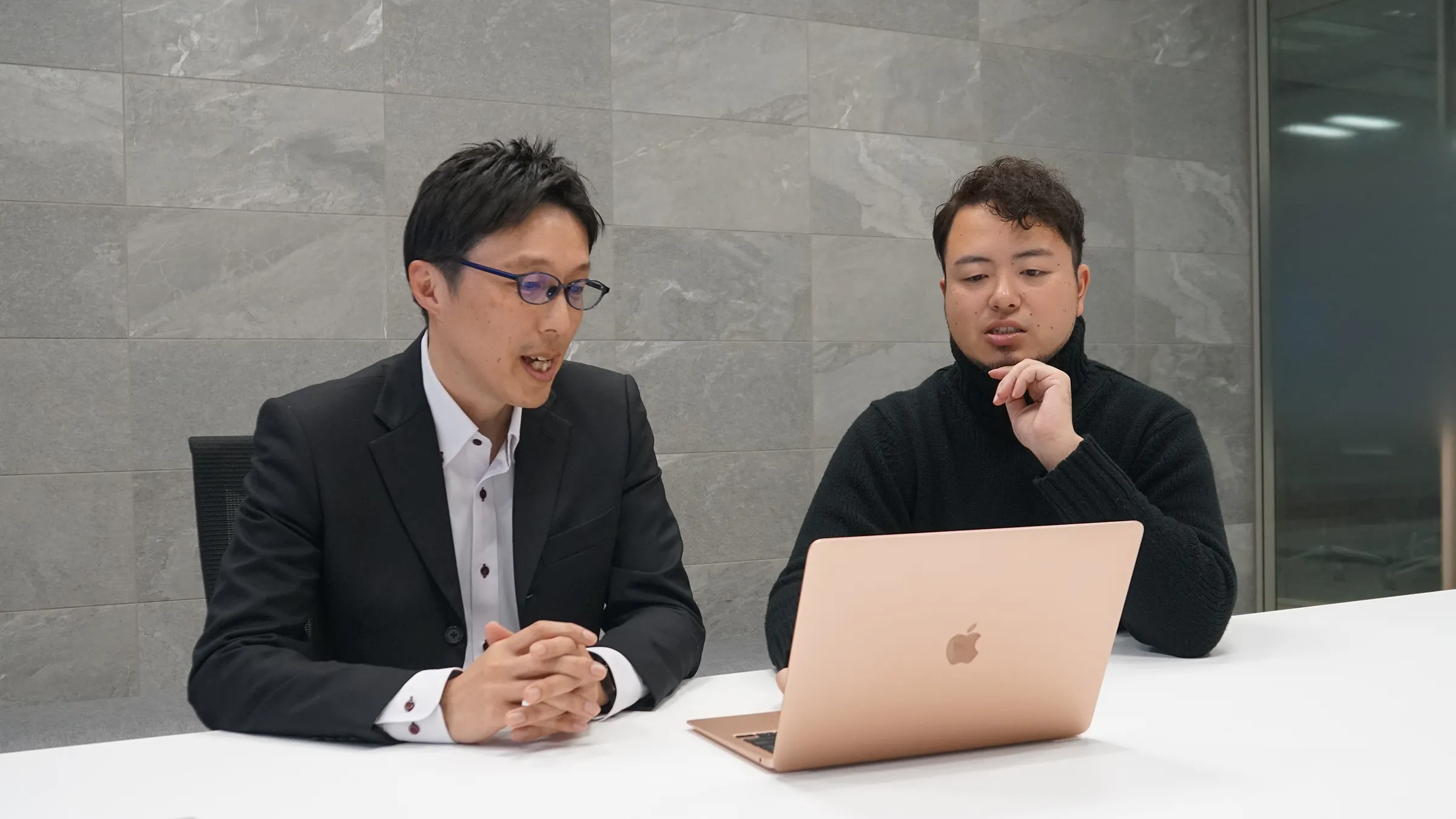
複雑な形状の画像検知率という壁に直面
―RistのDeep Counterを導入する前は、どのような課題や問題に直面していましたか?
楠野さま:部材の棚卸業務において、人の作業による間違いや、非効率なやり方による機会ロスが発生していました。そこで、物体検出技術を用いた棚卸のIT化に取り組みましたが、精度に欠ける部分があり、検知率が伸びないという悩みがありました。
ノーコード開発ツールでカウントアプリを作り、一時期は順調だったと思います。ただ、部材の種類を正しく判別するには、形状だけでなく断面も認識する必要があります。パッケージ化された画像処理AIには限界があり、検知率の面が大きな壁となったのです。そんな折に出会ったのが、Ristさんでした。
神野さま:今でも覚えていますが、自動認識総合展に足を運んだ際、Ristさんのブースに掲示されていたポスターを見て、「あ、これかもしれない」と思いました。もともとノーコードで開発した自社アプリでAI画像による物体検知をやっていた経緯もあって、「これを解決したかった」とピンときたので、Deep Counterに興味を持った次第です。
―複雑な形状の検知率改善はビジネス全体にどのように影響を及ぼしていましたか?
神野さま:もし仮にDeep Counterと出会っていなければ、今でも棚卸業務は人の手に頼っていたでしょうし、掛かる工数も時間も以前と変化なく、膨大なものになっていたと予想されるほどです。
長期的に見れば、これから日本は人口減少が本格化し、労働人口も少なくなっていきます。雇用が縮小していくなかいち早く、人の手でやる作業をデジタルに置き換えなければ、さまざまな部分にも悪い影響がおよびかねないと思っています。
楠野さま:そもそも、画像によって棚卸業務をやろうという発想が、時期尚早だったと捉えていたかもしれません。もしDeep Counterがなければ、このプロジェクト自体がどこかの時点で頓挫した可能性も十分に考えられます。
展示会で偶然見つけたテクノロジーに大きな期待を寄せた
―数あるソリューションの中から、なぜDeep Counterが選ばれたのでしょうか?
楠野さま:ICタグなどを使うRFIDを活用した棚卸業務のDXは、弊社内でも既に取り組んでおります。ただし、段ボールのような大型の対象物であれば十分ですが、中身の一点一点の個数管理にまでは対応しきれません。商品を個別でカウントするには、画像認識が必須だと思います。
しかし、画像認識も万能ではありません。形状が複雑で検知しにくい製品には不向きで、我々が扱うアルミ製の部材はまさに認識の難易度が高いものです。市販のカウントアプリでトライしてみたのですが、そういったツールが対象としている単純な形状ではないため対応しきれなかったというのが実情です。
だからこそ、カウントアプリの内製が必要でした。アプリ開発で重視したのが、「棚卸業務との連携性」「不規則に並ぶモノのカウントが可能かどうか」「カウント精度の向上」の3つです。
神野さま:従来使っていた物体検出のAIでも、単純形状なら問題はありませんでした。ですが、LIXILの扱う部材では、複雑な形状のものが大半を占めています。極端に低くなる物体検出のパーセンテージをいかにして、AIの画像認識で上げられるかが一番のポイントでした。
当時、「セグメンテーション」というAI学習を知らなかったのですが、展示会でRistさんのブースで事例を見て感動しました。インスタント麺の具材を正確に認識する事例です。まさに「これやな!」と、膝を打つ思いでした。
四角い形状だけではなく、不規則に散らばった状態にも対応できるAI画像認識技術があるのかという感動です。複雑な形状の品物が多いLIXILで、絶対に導入したいと感じました。
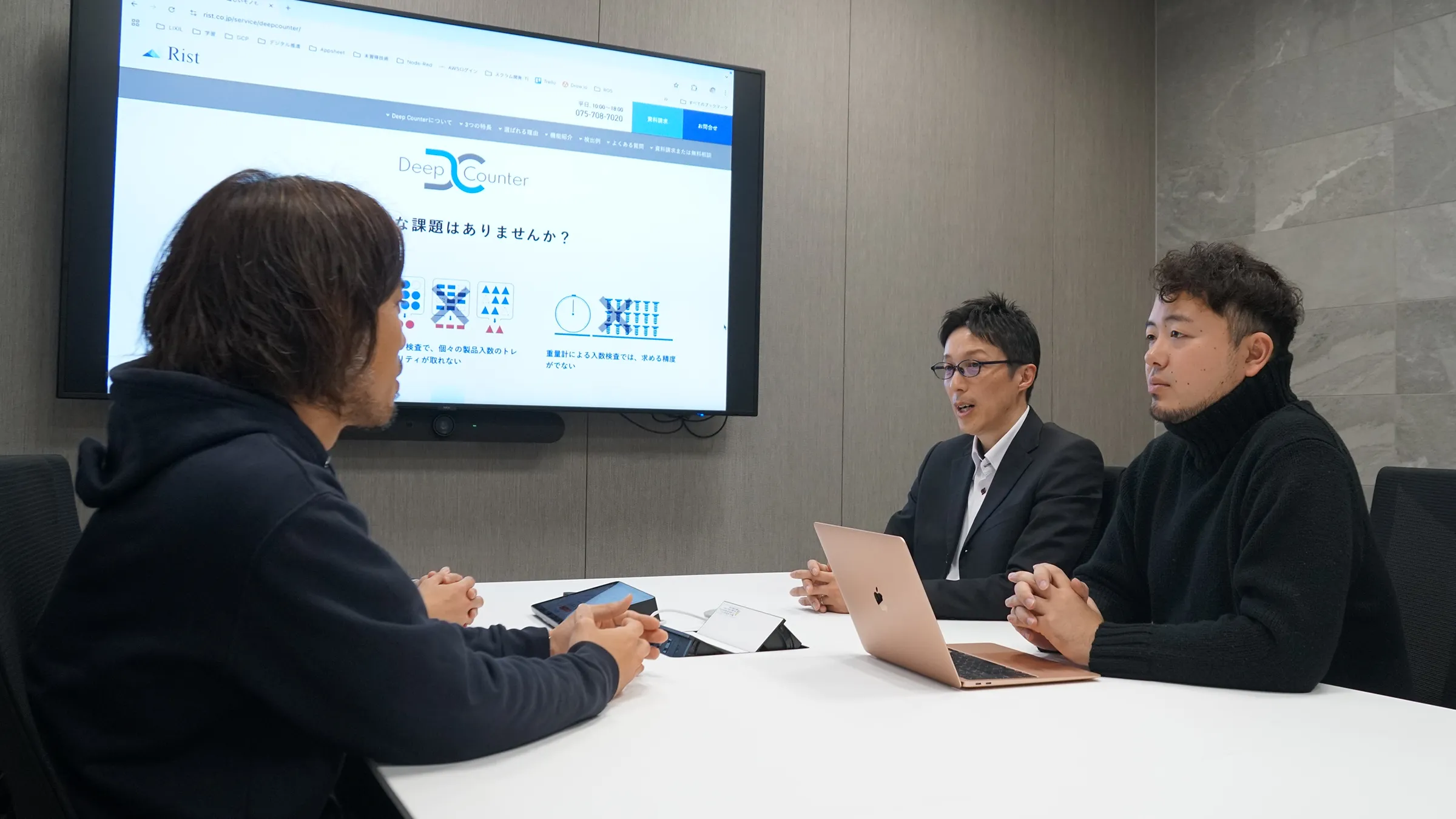
オールLIXILの観点、自走可能な状態の実現を重視した導入
―導入時に直面した課題や困難はありましたか?
楠野さま:システム的なところで最初にRistさんに相談したのが、既存システムとの連携についてです。ホワイトボードを使って説明し、たくさんのアイデアを出しながら議論させてもらいました。どのような形が連携に最適であるかを繰り返し議論させていただき、大変助かりました。
また、実際に導入する段階では、数万種類もの形に対応させる工程が欠かせません。1人では到底できない作業になるので、工場メンバーの理解を得て、各現場でアノテーションをするよう依頼しました。
画面上で「選択範囲をこう囲ったら精度が上がる」「逆に、こう囲ったら上手く検知されない」といったすり合わせを毎週行い、使い方の独自知見を取りまとめ続けたのです。その上で工場に展開したことで、誰もが使いこなせるようになったと思います。
―Deep Counterの導入プロセスで印象に残っていることを教えてください。
神野さま:もっとも苦労したのは、アルミ製の部材の断面が見えるようにするという環境的な要素をいかにしてクリアするかでした。アルミ製の部材の中には、全長が5メートルになるものもあり、ピッキング時につく傷を防止するため、1本ずつ不織布で全体を覆っています。垂れ下がった不織布が断面を隠してしまうため、画像検知が一筋縄ではいかない状態でした。
そこで、原材料のアルミ材を仕入れている工場と掛け合って、断面が見えるようにして欲しいと要望しました。ですが、材料工場からすれば、断面が見えるように不織布を整えるというひと手間が生じます。言い換えると、我々としては画像検知によって工数が減りますが、工場にとっては工数が増えるということ。オールLIXILの観点から考えて、お互いにとってメリットがなければ、業務効率化になりません。
そのため、材料工場の製造工程にも画像検知の技術が非常に有効であるという説明をさせていただきました。我々と同様に、材料工場内での他の部材や製品の棚卸業務に画像検知を使ってみてはどうか、と。何度も相談を繰り返し、Ristさんにもいろいろと動いてもらって、導入に至って良かったです。
現場業務の省力化だけでなく、管理部門も業務改善に成功
―Deep Counter導入に対する社内の反応はいかがでしたか?
神野さま:これまでは手作業だった工程が、Deep Counterでカウントできるようになりました。そのため現場からは、「人が書く」作業がなくなり、「数える」作業もいらなくなり、大幅な時間短縮が図れた、とても喜ばれています。
また、棚卸データを基幹システムに入力する作業に、以前は毎日30~40分をかけていましたが、今はわずか1~2分で完了します。現場だけでなく、間接部門の業務効率まで図れました。
―Deep Counter導入によって、どの程度の業務改善が図れましたか?
楠野さま:数値としては、棚卸業務1件に対して、約10分程度の工数削減です。試験導入で102ヵ所の棚卸業務に採用し、月間17時間の時間短縮を達成しました。
神野さま:今でこそ、Deep Counterによる成果はとても大きなものとなっていますが、最初は「ちょっとやってみようか」という程度の期待感でスタートしました。徐々に構想通りに実用化できる目途が立ち、いくつかの部署も連携して形にすることができました。
社内SNSで取り組みを報告すると、本部から全社展開するように依頼が来たり、会社の広報活動でも話題として取り上げられたりと、雪だるま式に注目度が高くなっていった経緯があります。最初は小さな相談事だったものが、自分たちの発想でここまで大きくできたという確かな手応えを感じています。
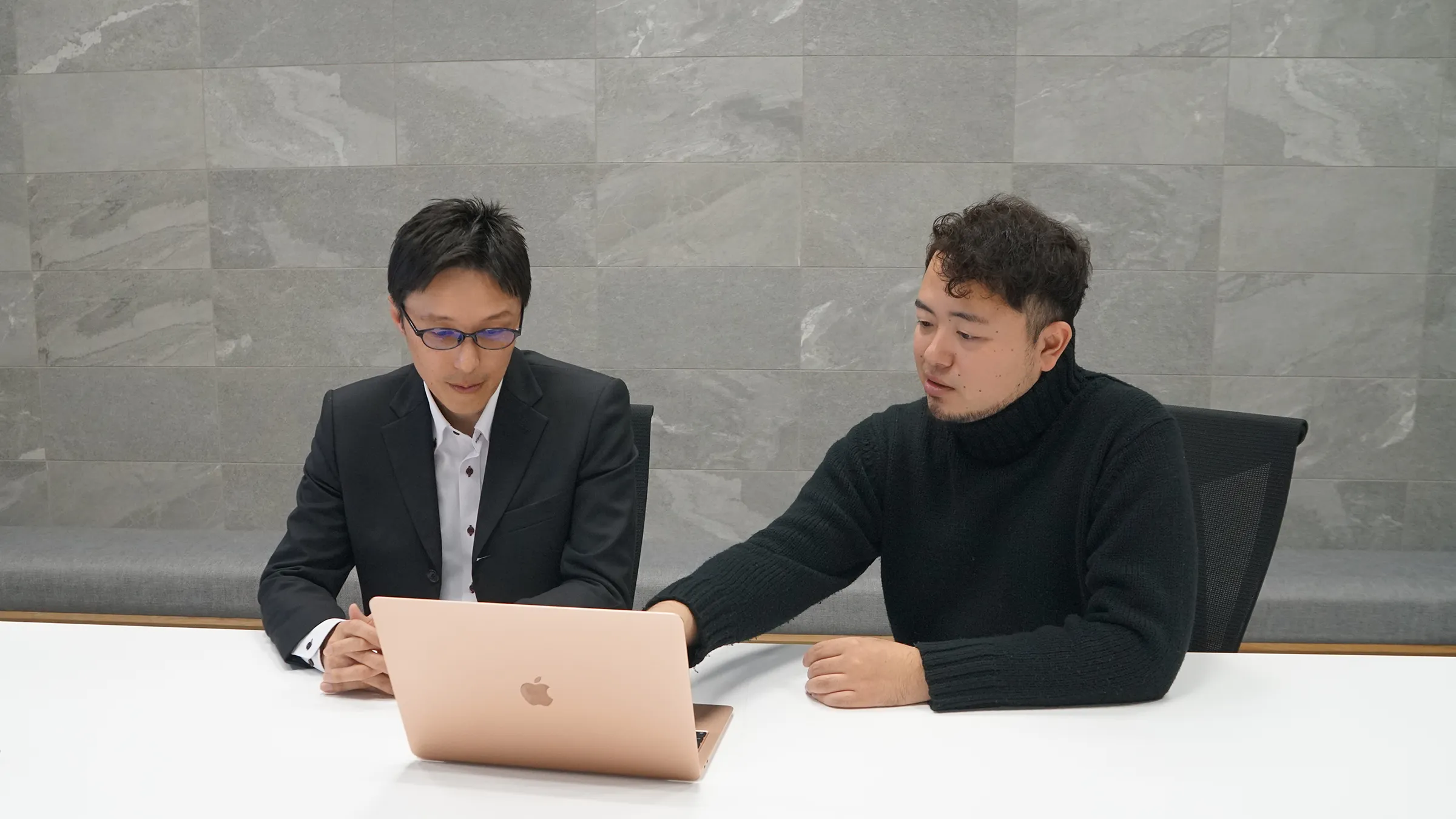
成果を出すことはもちろん、再現性と横展開を考え続ける
―導入に成功されたポイントはどこにあったのでしょうか?
神野さま:まずはモデル工場でノウハウを作り、パッケージとして他の工場にも広めていった点です。抵抗なく受け入れてもらうために、時間をかけて学習データを蓄積したことも、成果につながっています。
AIに触れたことがない社員が多いなかで、先に導入した工場が責任を持って成果を出し、再現性を担保することが、スムーズに横展開していく上で非常に重要であると実感しました。
楠野さま:違う観点では、既存アプリとの連携だったと思います。棚卸業務そのものはアプリを使ってできますが、それだけでは手作業での工数と大きく変わりません。Deep Counterと連携できて初めて、大幅な省力化が可能になりました。
Ristさんが、前例のない中でDeep CounterをAIエンジンとして弊社に提供できるよう試行錯誤していただけたことは、大きなポイントです。
発想を止めずにDXの機会を狙い続ける
―今後、Deep Counterをどのように活用していきたいと考えていますか?
神野さま:つい最近のことですが、Ristさんのサイトで板状の対象物もカウントできるという事例を見つけました。「これなら鋼板にも使えるかも」と思ったところです。現在のアルミ製の部材だけでなく、他の資材にも使えるのではと考えています。
また、今は棚卸業務でのカウント作業に活用していますが、LIXILの製品には部品箱があり、その品質保証業務にも転用できないかと構想を練っている最中でもあります。まだまだ多くの部分に導入していくつもりなので、相談させていただくことがきっとあると思います。
楠野さま:個人的には、もっとシステム連携できないかと考えています。今の棚卸用アプリは、スマホで画像を撮影してシステムにデータを送り、システムが検知・カウントした結果を手元のアプリに通知される仕組みです。
現状のDeep Counterでは、AIの学習データづくりについての補助機能はありますが、都度ユーザが行う必要があります。今後はAIの判定結果を人間が確認した際の修正機能と、その修正した結果を蓄積して学習データとして活用できる機能があると良いなと考えています。
また、会社としてクラウドサービスの利用を進めておりますので、Deep Counterについてもクラウド版の開発をお願いしたいと思っていました。
Ristさんに相談したところ、すぐに「クラウド版のベータ版が完成しました」と連絡をいただいたのですが、いつでもタイムリーに対応してくださるので、とても助かります。
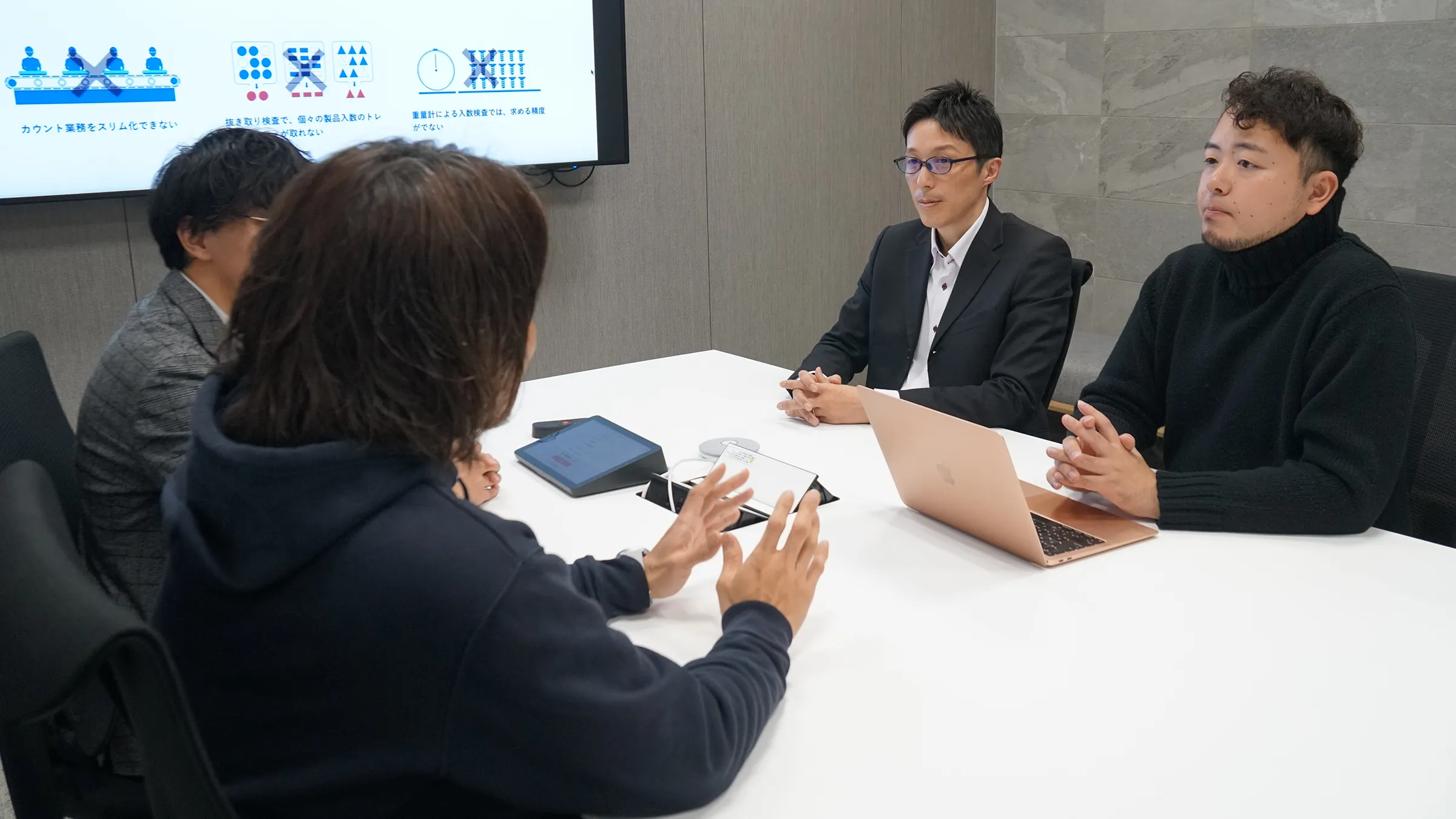
AIに詳しくなくても、やってみる価値は十分にある
―同様の課題を持つ他社に対して、弊社のプロダクトを推薦するとしたら、どのように紹介されますか?
楠野さま:我々と同じように、ぜひチャレンジしていただきたいですね。触ってみれば、きっとカウント精度の高さを実感できるはずです。
最初は、自社が扱う製品の形状的に難しいと感じる人が多いと思います。実際に我々もそうでした。今回の事例で取り上げたアルミ製の部材は、断面を視認できないとカウントされないという課題もあったぐらいです。ですが、PoCの段階ですぐにカウント精度が極めて高いことに気づき、カスタムやチューニングもできることに大きな可能性を見出しました。
実装までの過程も議論を繰り返しながら形にしてきましたので、さまざまな分野・用途にDeep Counterは利活用できるはずです。Ristさんのサポートもあって、プロジェクトはいったん動き出せば、あっという間にびっくりするほど速く進んでいくので、まずは試してみるのがおすすめです。
神野さま:複数の工場や本部を巻き込む大規模なAI導入を検討しているなら、ぜひRistさんに相談してみてください。Ristさんは導入ステップやハードルの乗り越え方など様々なノウハウを持っているので応えてくれます。
AIに対してハードルの高さを感じる方もいらっしゃると思いますが、専門的な知識がなくても導入できるのが今の時代です。最初はよく分からなくても、少しずつできることが分かったり、さらに試してみたいやり方などが見つかったりしていくと思うので、まずはやってみる価値が十分にあるのではないでしょうか。
―貴重なお時間をありがとうございました。
本プロジェクトは、以下の2社によるものです。
導入支援:京セラコミュニケーションシステム株式会社
Deep Counterの提供元:株式会社Rist